JASPER XIV
Share
Lightweight Safety Helmet
- Mallcom Jasper XIV non-ventilated zip adjusted Industrial safety helmet with PP shell, LDPE harness & chin strap.
- It is light weighted, durable helmet that meets a wide range of standard performance requirements
- It is available with a choice of rachet or zip adjustment for adaptability
- It is confirmed for use at temperatures ranging from -10°C to + 50°C
- It provides superior protection to the skull and excellent durability
- This helmet complies with the PPE REGULATION 2016/425 as a CATEGORY II
- Colors available: Yellow, White, Bue, Red, Green, Orange & Violet

Impact
Projectiles
Bump
Select Color
JASPER XIV

Size Chart
How to Measure
JASPER XIV

JASPER XIV


IS 2925
Delivery & Services

Easy Return
with our 15 days return poicy
Regular price
Rs. 0
Sale price
Rs. 0
Regular price
Tax included.
Shipping calculated at checkout.












ABOUT THE DESIGN
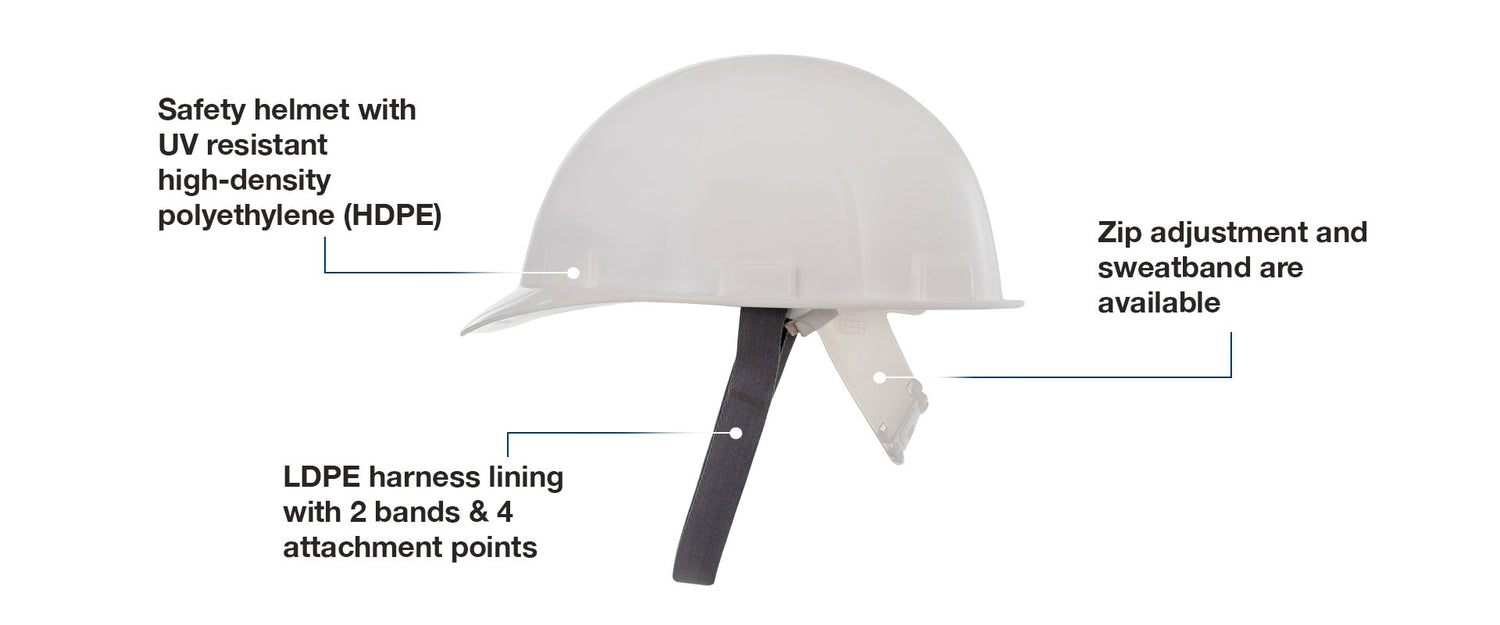
USEFUL IN THESE INDUSTRIES
IRON & STEEL
CONSTRUCTION
CEMENT
MANUFACTURING
REPAIRS & MANTENANCE

The helmet shall be mounted on a wooden head form of appropriate size. The wooden striker weighing 3 kgs and having a horizontal striking face of 180 mm X 180 mm, shall be raised to a clear height of 1.5 m above the point of contact with the helmet and allowed to fall freely. A record of the force transmitted during impact shall be made.
Mount helmet on an appropriate headform. Drop freely a plumb bob of 500 gms mass with a conical steel point having an included angle of 36 degrees and a spherical point radius of not more than 0.5 mm from a clear height of 3.0 m with the pointed end downwards on to the top of the crown of the helmet. Examine the helmet for piercing or denting, failure of any integral parts etc.
With the helmet upside down and the burner angled at 45 degrees to the vertical, the end of the flame shall be applied to the outside of the shell at any suitable point between 50 & 100 mm from the crown for a period of 10 seconds. The plane tangential to the test point shall be horizontal. The shell shall be examined for flaming 5 seconds after removal of the flame.
Invert the helmet and place it on a frame in a suitable container. With a solution of 6g/l of water, fill the container and the helmet to within 12mm of the junction of the brim and the dome, or if the helmet is provided with holes to a depth of 12 mm below the holes. Allow the helmet to remain in the solution for a period of 18 to 24 hours and maintain the temperature of 25 degrees to 35 degrees Centigrade during this period. Then apply an alternating voltage of 2000 V at 50Hz for 1 minute between electrodes placed in the solution inside and outside the helmet respectively. If no electrical breakdown occurs, disconnect the high voltage supply and connect a milliammeter in the circuit on each side of the electrode. Raise the test voltage slowly observing the ammeter reading, until the applied voltage is 2000V.
The sample used for shock absorption is used for carrying out this test. Weigh the sample (full shell). Immerse for 24 hours in water at a temperature of 25 to 35 degrees centigrade. Remove from water, dry the surfaces by wiping them and weigh again. Report the average gain in mass as a percentage.
Place the shell in an oven maintained at a temperature of 93 degrees centigrade. The shell shall be shielded from direct radiation during the test. Remove the shell from the oven and examine for separation, distortion or softening.
Product Features
ABOUT THE DESIGN
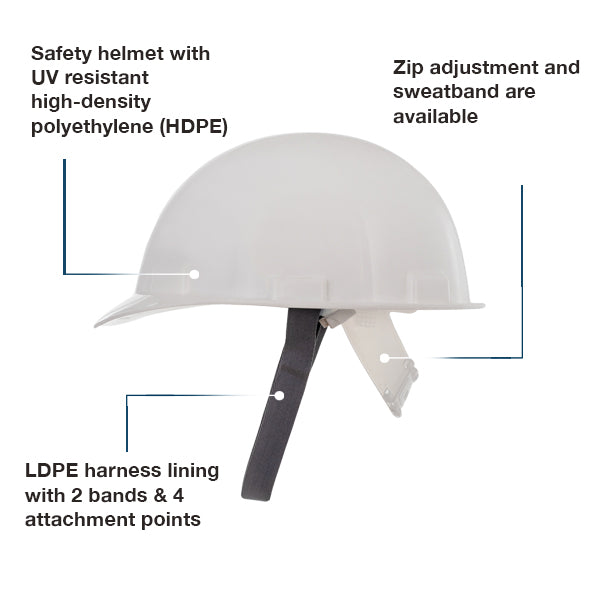
USEFUL IN THESE INDUSTRIES
IRON & STEEL
CONSTRUCTION
CEMENT
MANUFACTURING
REPAIRS & MANTENANCE
Product Details
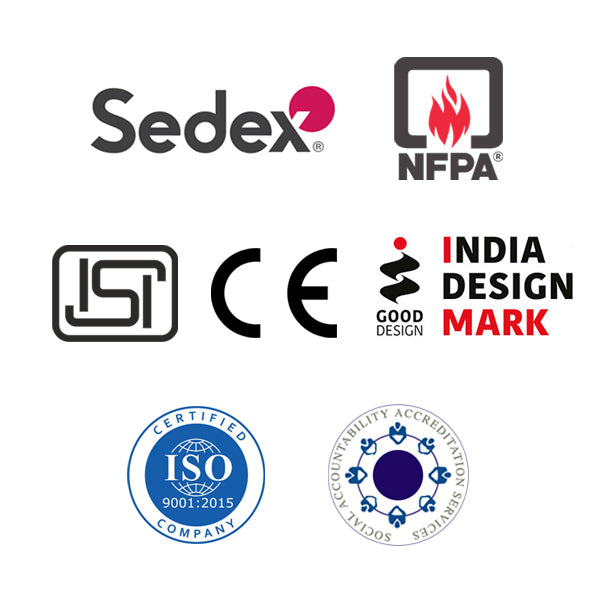
Tests
The helmet shall be mounted on a wooden head form of appropriate size. The wooden striker weighing 3 kgs and having a horizontal striking face of 180 mm X 180 mm, shall be raised to a clear height of 1.5 m above the point of contact with the helmet and allowed to fall freely. A record of the force transmitted during impact shall be made.
Mount helmet on an appropriate headform. Drop freely a plumb bob of 500 gms mass with a conical steel point having an included angle of 36 degrees and a spherical point radius of not more than 0.5 mm from a clear height of 3.0 m with the pointed end downwards on to the top of the crown of the helmet. Examine the helmet for piercing or denting, failure of any integral parts etc.
With the helmet upside down and the burner angled at 45 degrees to the vertical, the end of the flame shall be applied to the outside of the shell at any suitable point between 50 & 100 mm from the crown for a period of 10 seconds. The plane tangential to the test point shall be horizontal. The shell shall be examined for flaming 5 seconds after removal of the flame.
Invert the helmet and place it on a frame in a suitable container. With a solution of 6g/l of water, fill the container and the helmet to within 12mm of the junction of the brim and the dome, or if the helmet is provided with holes to a depth of 12 mm below the holes. Allow the helmet to remain in the solution for a period of 18 to 24 hours and maintain the temperature of 25 degrees to 35 degrees Centigrade during this period. Then apply an alternating voltage of 2000 V at 50Hz for 1 minute between electrodes placed in the solution inside and outside the helmet respectively. If no electrical breakdown occurs, disconnect the high voltage supply and connect a milliammeter in the circuit on each side of the electrode. Raise the test voltage slowly observing the ammeter reading, until the applied voltage is 2000V.
The sample used for shock absorption is used for carrying out this test. Weigh the sample (full shell). Immerse for 24 hours in water at a temperature of 25 to 35 degrees centigrade. Remove from water, dry the surfaces by wiping them and weigh again. Report the average gain in mass as a percentage.
Place the shell in an oven maintained at a temperature of 93 degrees centigrade. The shell shall be shielded from direct radiation during the test. Remove the shell from the oven and examine for separation, distortion or softening.